Zcat7
Well-known member
- Joined
- Apr 12, 2010
- Messages
- 662
- Reaction score
- 3
- Location
- Oxfordshire
- Year of Your Van(s)
- 1972
- Van Type
- Crossover
I was asked to post a few piccies of my 1776 build. I went down this road after my low mileage 1641 SSP engine, with Brailian AS41 case, cracked around the oil cooler pedestal. I'm using a new Auto Linea case, bored for 90mm barrels and pistons, an Engle 100 cam and all other standard parts from the original engine.
AS41 block complete with crack. You can see where I tried to fix it with a JB weld. I think I know why this failed but more on that later...
Engine mid stripdown
Old and new cases
Crankshaft out and stripped. Engle cam mated to it's drive gear.
Engle 100 Cam assembled and clearanced (requires old style oil pump and bolt heads grinding down to clear)
Journals polished with 800 and 1000 grit and conrods installed
Fully loaded crank installed into case. New lifters awaiting camshaft
2 halves almost ready to be assembled
All bolted up
The casting has a nice finish and the milled surfaces are polished really nicely. For those eagle eyed among you, the engine has been turned since the dizzy drive was installed!
New barrels and pistons, I went for cast as I don't plan on a turbo!
Shiney and new...
First piston/barrel goes on...
Followed by the other 3!
Heads bored out for the larger barrels and given a light de-coke (there wasn't much in there)
Heads installed! But not for long... I forgot to clip in the 2 small pieces of tinware that go under the barrels so off they came again...
The dreaded oil cooler installed. If I had a pound...
And that's it for now. More to follow soon...
Neil
AS41 block complete with crack. You can see where I tried to fix it with a JB weld. I think I know why this failed but more on that later...
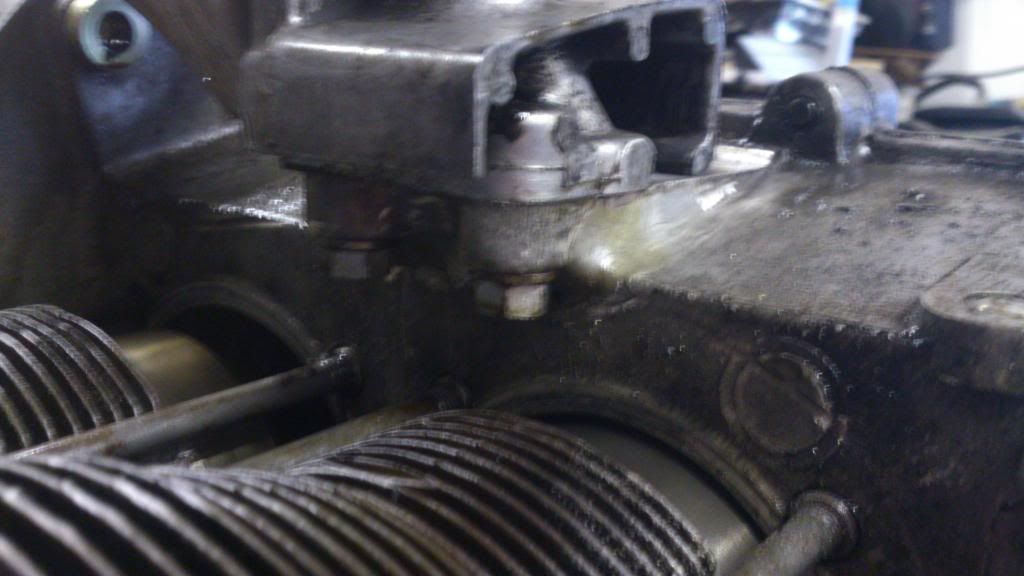
Engine mid stripdown
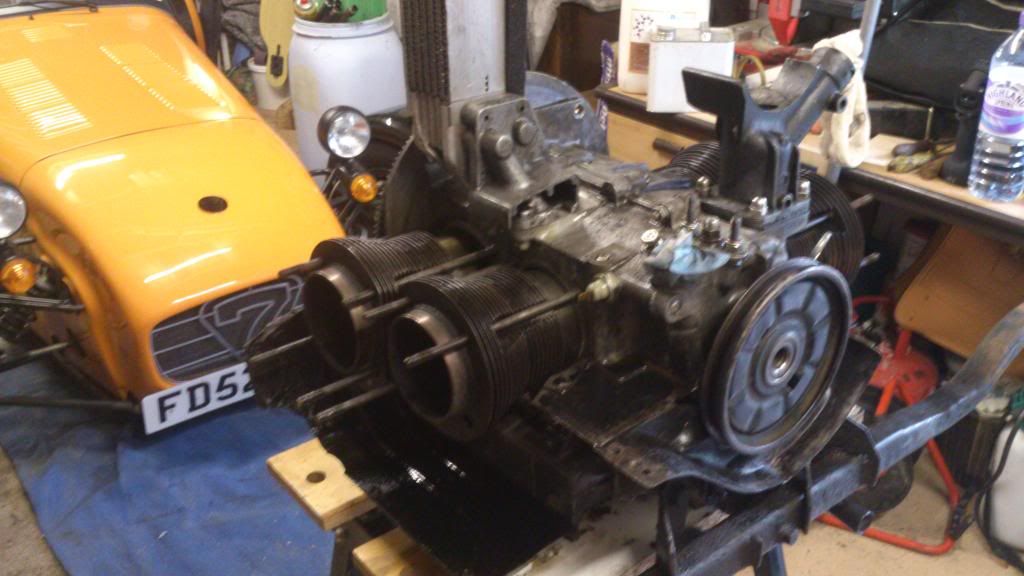
Old and new cases
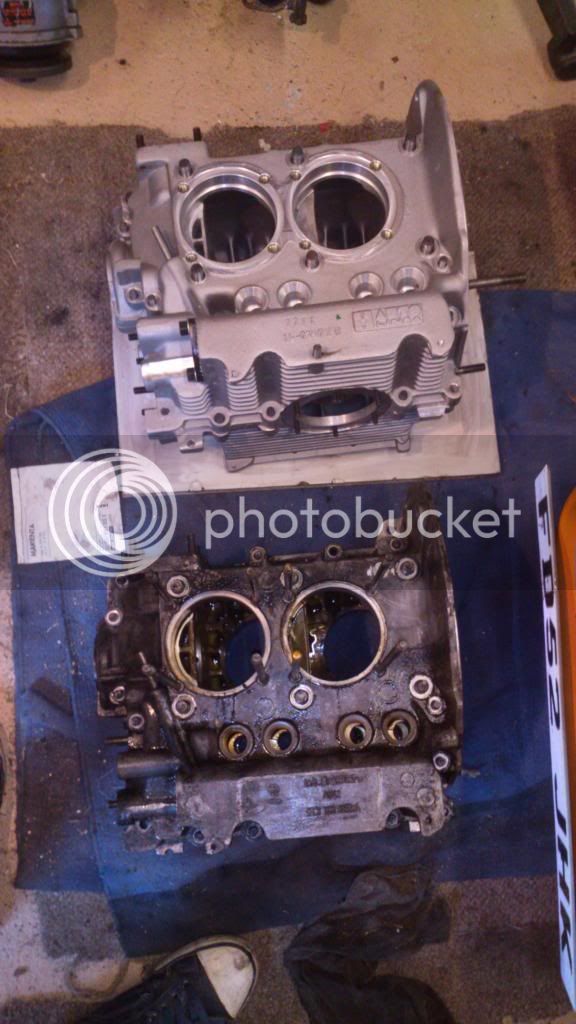
Crankshaft out and stripped. Engle cam mated to it's drive gear.
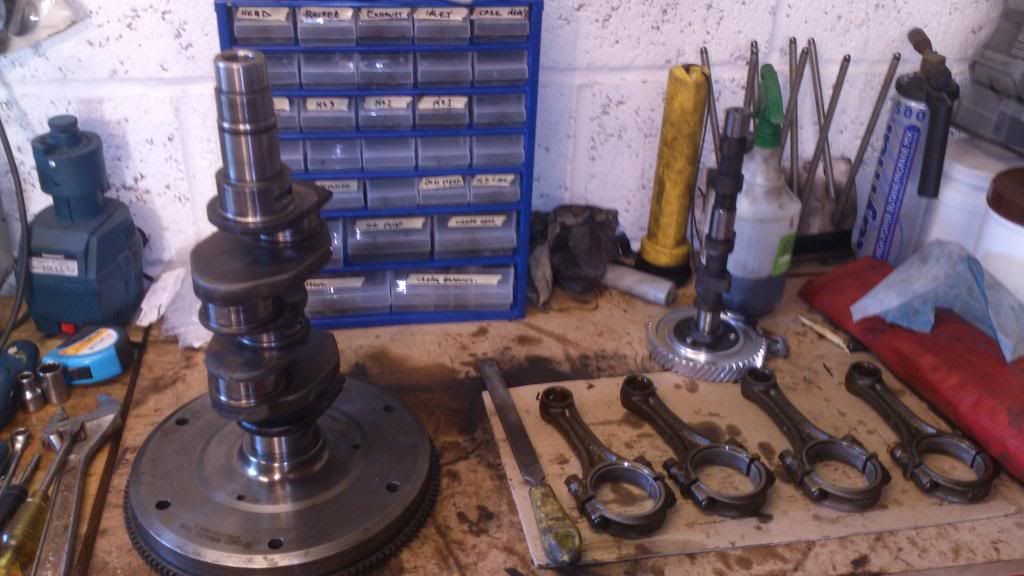
Engle 100 Cam assembled and clearanced (requires old style oil pump and bolt heads grinding down to clear)

Journals polished with 800 and 1000 grit and conrods installed
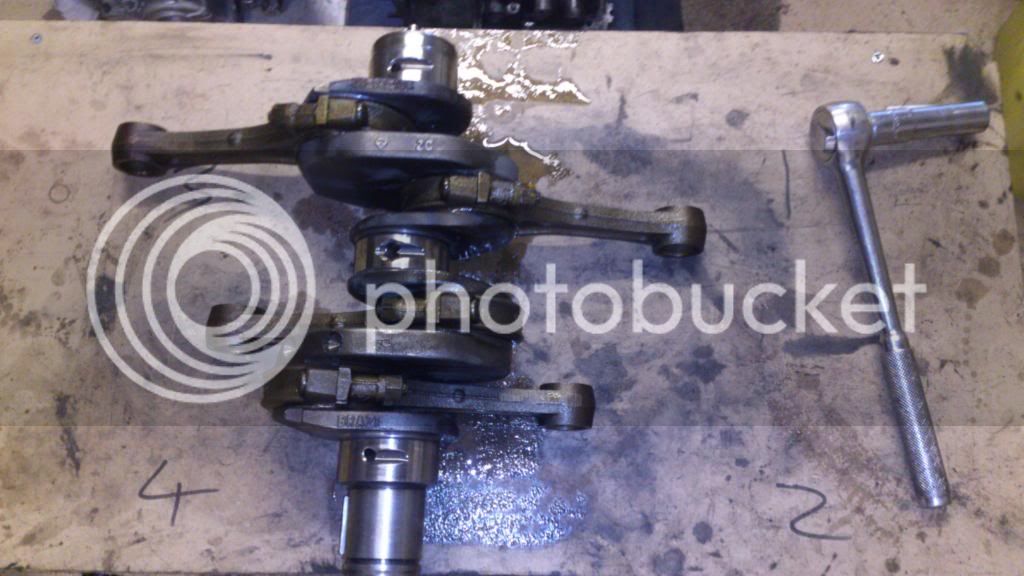
Fully loaded crank installed into case. New lifters awaiting camshaft
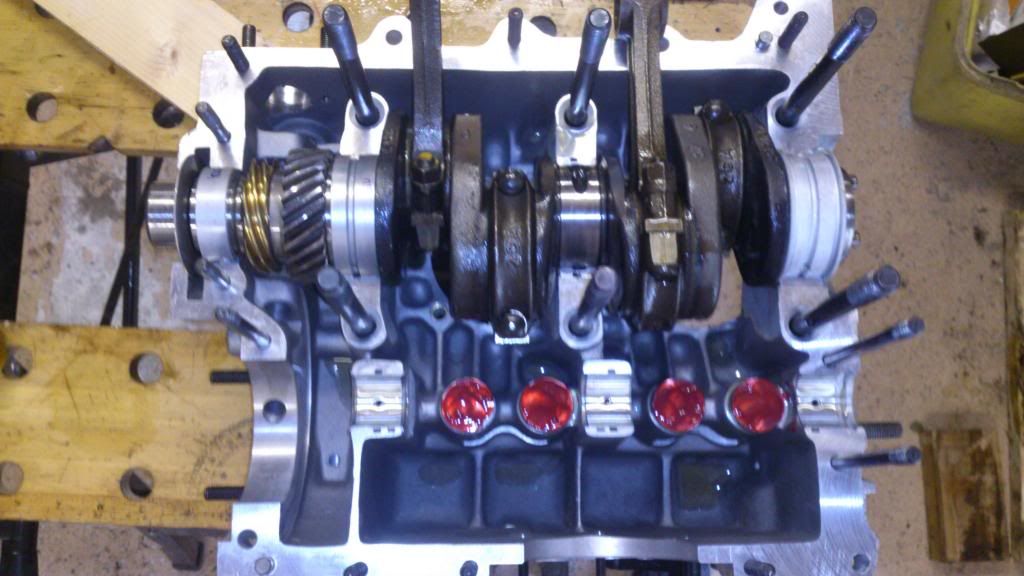
2 halves almost ready to be assembled
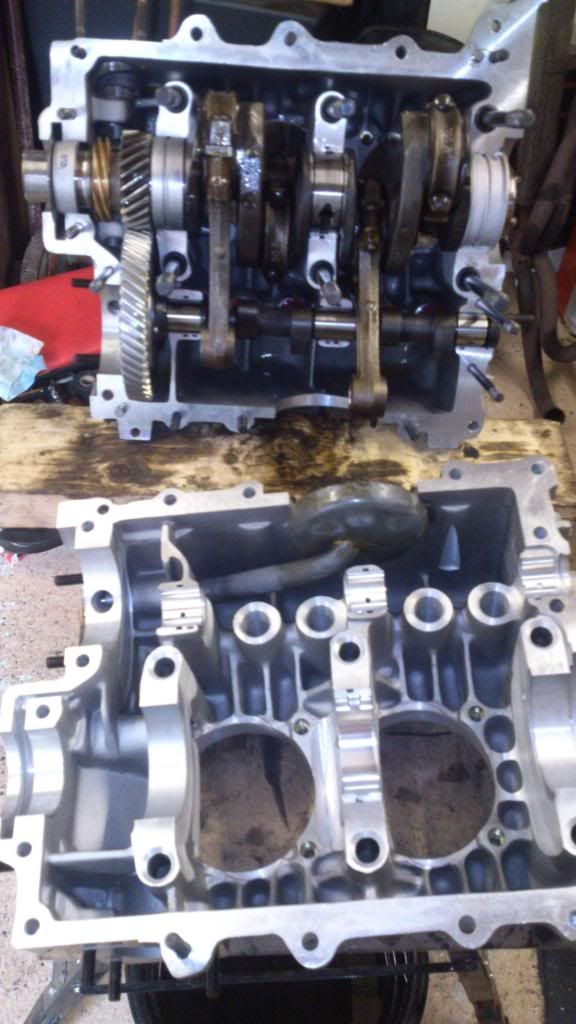
All bolted up



The casting has a nice finish and the milled surfaces are polished really nicely. For those eagle eyed among you, the engine has been turned since the dizzy drive was installed!

New barrels and pistons, I went for cast as I don't plan on a turbo!

Shiney and new...
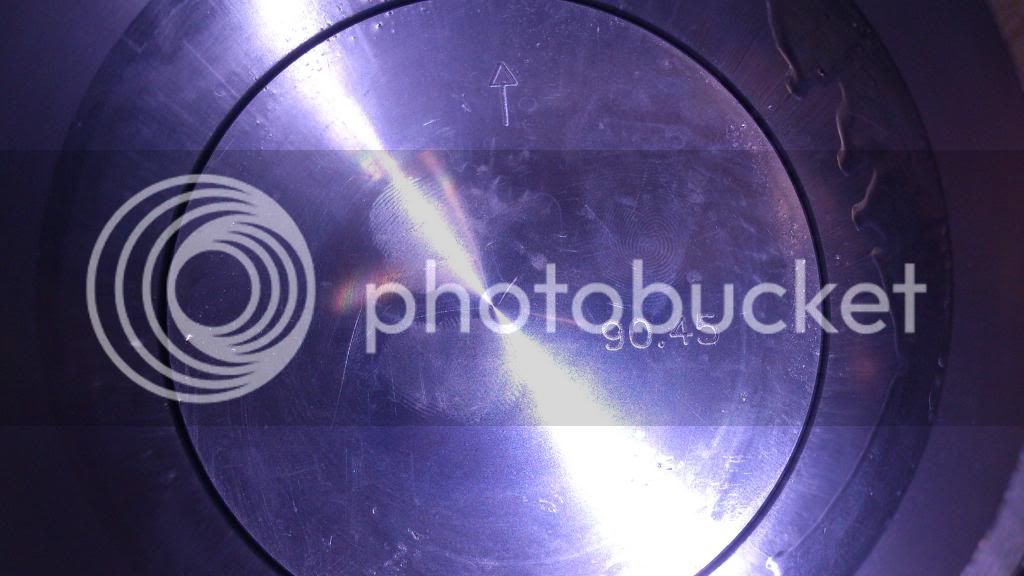
First piston/barrel goes on...
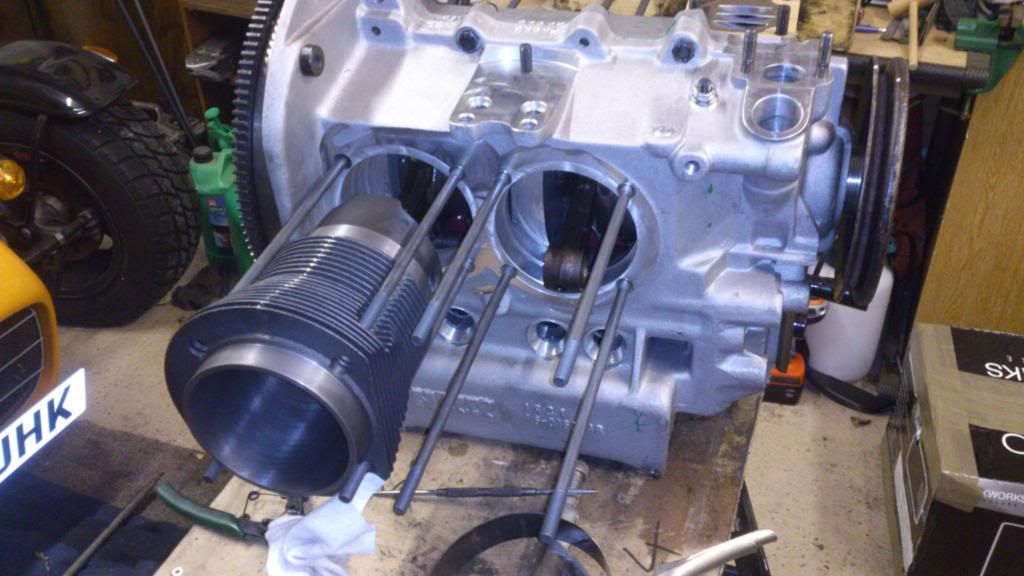
Followed by the other 3!

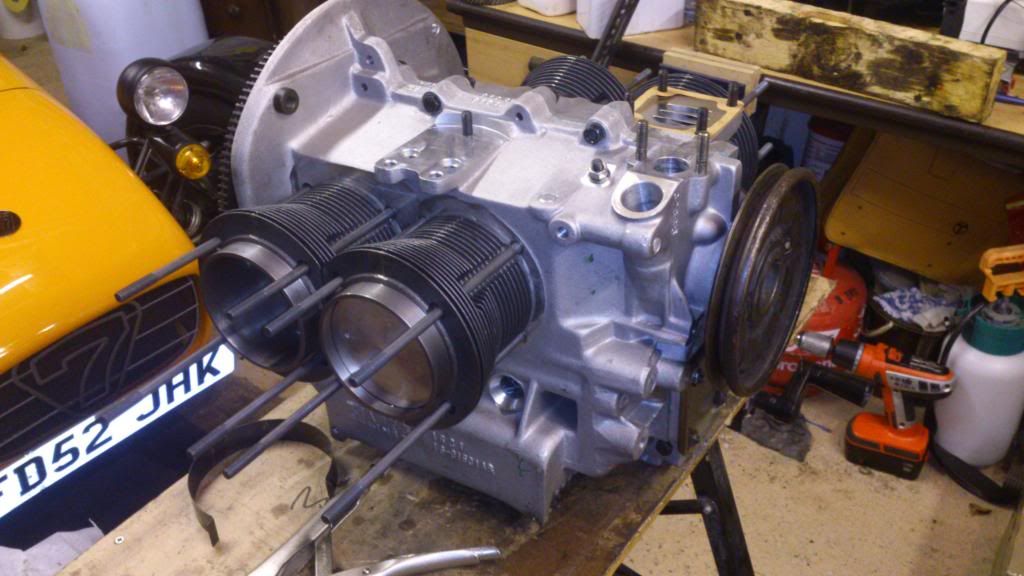
Heads bored out for the larger barrels and given a light de-coke (there wasn't much in there)

Heads installed! But not for long... I forgot to clip in the 2 small pieces of tinware that go under the barrels so off they came again...
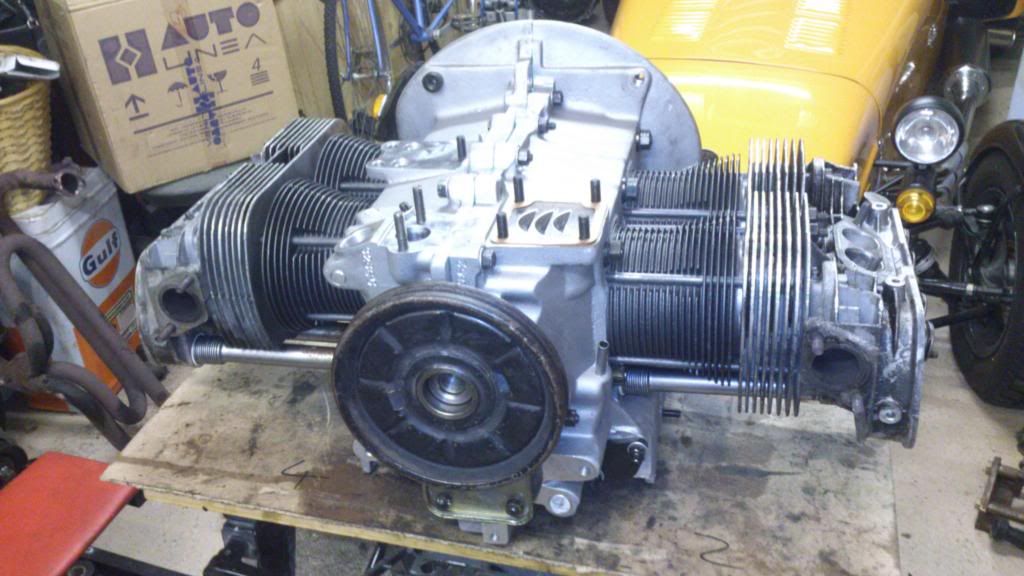
The dreaded oil cooler installed. If I had a pound...

And that's it for now. More to follow soon...
Neil