Bay_Buster
Well-known member
- Joined
- Mar 9, 2013
- Messages
- 84
- Reaction score
- 3
Hi everyone. I'm in the process of replacing the O/S main chassis rail on my RHD '68. The replacement is from a LHD so I'm shifting all the necessary gubbins over/making new ones to suit. I've just finished the steering box mount, now it's the turn of the metalwork associated with the throttle linkage. Having chopped the old throttle linkage out it's clear it wears quite a lot over time as it's just metal rubbing metal where it passes through the chassis. Here's a photo before I chopped it out so you know what I mean...
The weird looking welded metal on the top there is a crude jig so I could replicate the offset of the two arms each end of the linkage accurately when the new one is built. Anyway...
So when I go about building my new linkage I was thinking of using two housed bearings for the shaft to eliminate any wear. Something similar to this type of thing...
http://simplybearings.co.uk/shop/Ho...+Housing+with+1+inch+Insert/product_info.html
Just wondered if anyone had already solved this problem, or has any suggestions before I dive in! It's sure going to be fun fabbing up all that new metalwork accurately from scratch anyhow :?
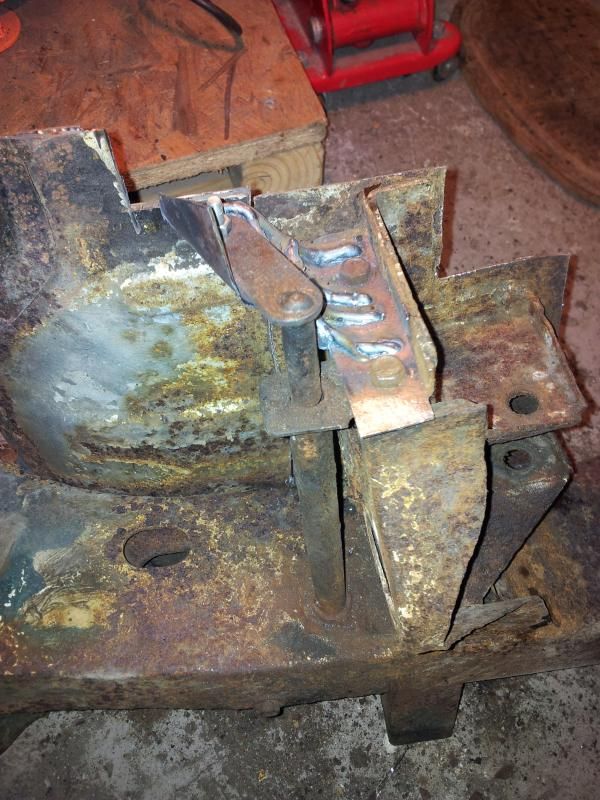
The weird looking welded metal on the top there is a crude jig so I could replicate the offset of the two arms each end of the linkage accurately when the new one is built. Anyway...
So when I go about building my new linkage I was thinking of using two housed bearings for the shaft to eliminate any wear. Something similar to this type of thing...
http://simplybearings.co.uk/shop/Ho...+Housing+with+1+inch+Insert/product_info.html
Just wondered if anyone had already solved this problem, or has any suggestions before I dive in! It's sure going to be fun fabbing up all that new metalwork accurately from scratch anyhow :?