The gearbox was an expensive option for me despite costing very little to purchase initially (circa £350) - SubaruGears is an effective solution if you want to run a 5 speed box that has the correct ratios related to the engine output and has a variable speed sensor mounted to it that talks to the ECU which when running an aircooled 4 speed box can cause some erroneous running issues as the signal is missing. It also does use a hydraulic slave/master system but more of that later.
However many peeps successfully run standard 3/6 ribs hooked up to Subaru motors using an adaptor plate and a box of tricks that fools the ECU into getting the correct signal. The adaptor plate is far more straightforward than using an Impreza box however I wanted to do the conversion once and not have to revisit it as knowing my luck I would have destroyed the first aircooled gearbox I used and then wouldn’t have had use of the bus whilst it was away getting rebuilt/repaired and I still wouldn’t have 5 gears and nice quiet cruising.
So after Nick converted the box I went about installing the universal joint that would facilitate the mating of the Subaru output shaft to the vw shift rod. It’s a super beetle steering shaft for anyone who is interested.
As you can see there is a significant amount of movement in the UJ which I came to realise was necessary.
The Subaru box is still installed to the original mounting point as per the 3 rib box however it uses a cradle to facilitate this attachment with the OG mount installed onto this.
Next on the agenda was to install the cups for the drive shafts. They attach to the output shafts on the gearbox and are pinned into place.
Due to the differential being flipped to the other side of the box the gearbox oil dipstick or rendered obsolete so a sightglass is included
Also the nosecone is cut and welded to accommodate the internal changes
After filling with oil this pretty much was the gearbox ready for installation. Nick Tune did all the hard work of actually converting the box, setting the backlash and grinding the clearances to tolerance.
If you grind too much you can make small holes in the casing that frustratingly leak gearbox oil - can’t they Matt?
Sent from my iPhone using Tapatalk
However many peeps successfully run standard 3/6 ribs hooked up to Subaru motors using an adaptor plate and a box of tricks that fools the ECU into getting the correct signal. The adaptor plate is far more straightforward than using an Impreza box however I wanted to do the conversion once and not have to revisit it as knowing my luck I would have destroyed the first aircooled gearbox I used and then wouldn’t have had use of the bus whilst it was away getting rebuilt/repaired and I still wouldn’t have 5 gears and nice quiet cruising.

So after Nick converted the box I went about installing the universal joint that would facilitate the mating of the Subaru output shaft to the vw shift rod. It’s a super beetle steering shaft for anyone who is interested.
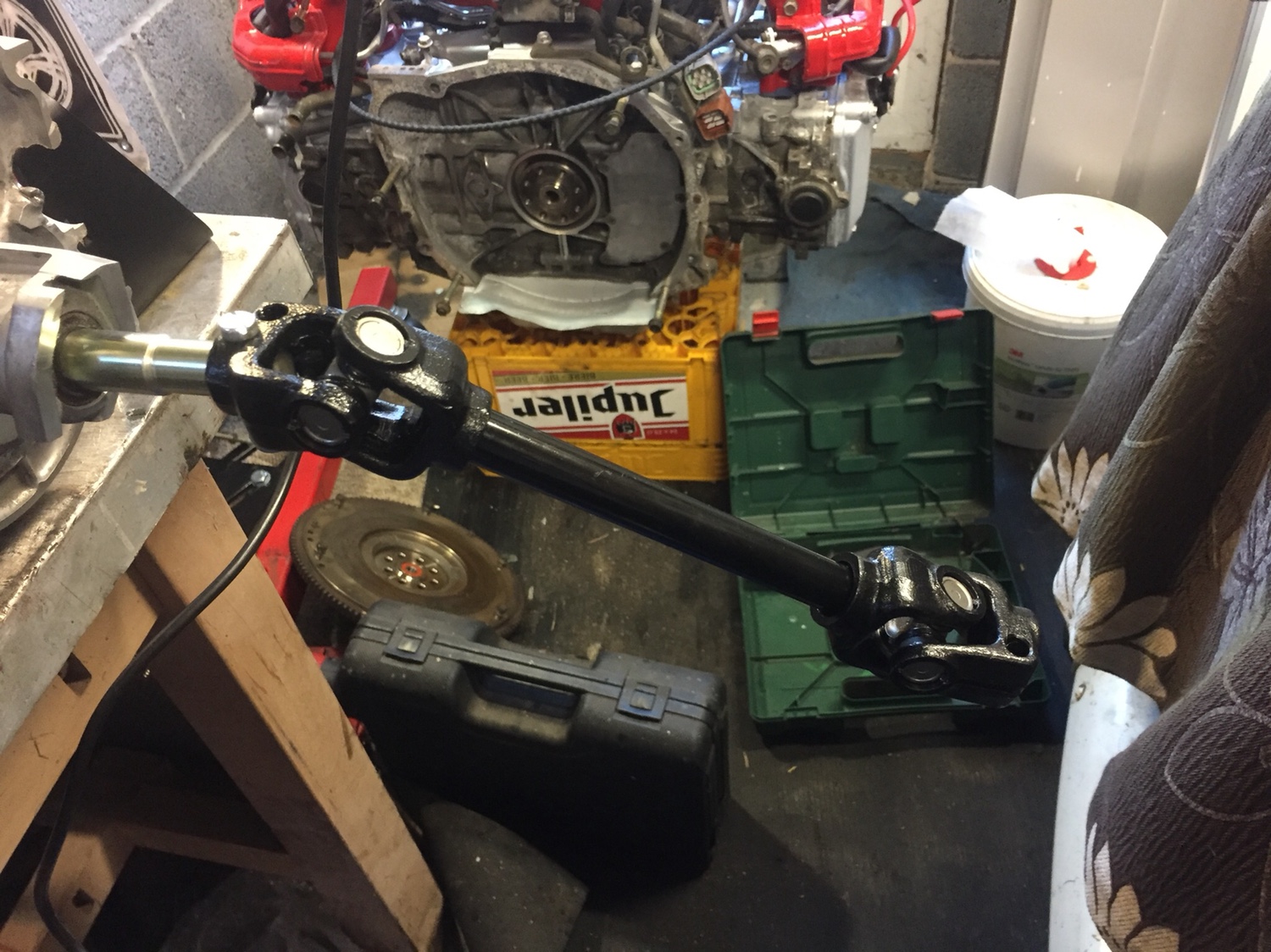
As you can see there is a significant amount of movement in the UJ which I came to realise was necessary.
The Subaru box is still installed to the original mounting point as per the 3 rib box however it uses a cradle to facilitate this attachment with the OG mount installed onto this.

Next on the agenda was to install the cups for the drive shafts. They attach to the output shafts on the gearbox and are pinned into place.
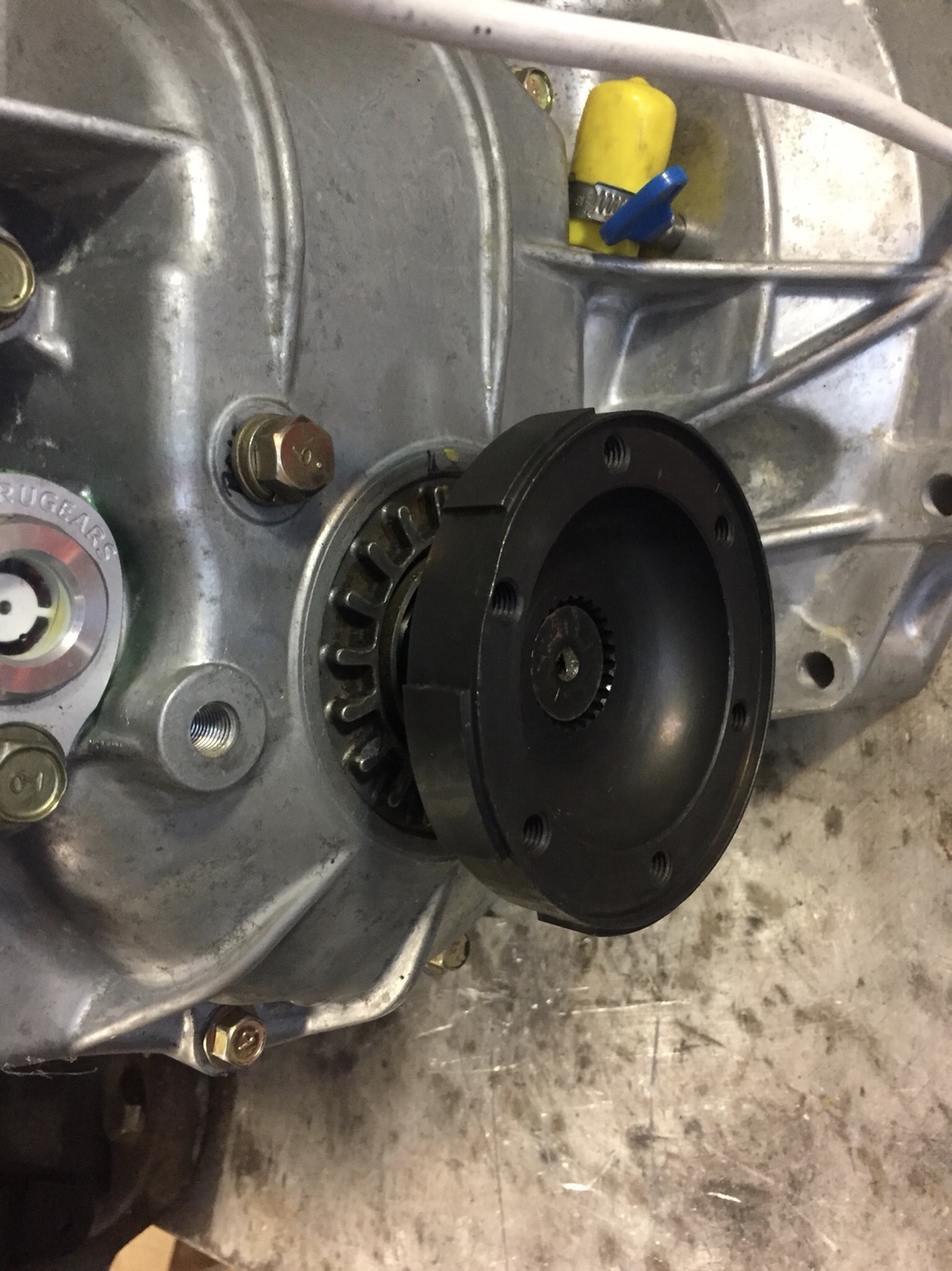

Due to the differential being flipped to the other side of the box the gearbox oil dipstick or rendered obsolete so a sightglass is included

Also the nosecone is cut and welded to accommodate the internal changes

After filling with oil this pretty much was the gearbox ready for installation. Nick Tune did all the hard work of actually converting the box, setting the backlash and grinding the clearances to tolerance.
If you grind too much you can make small holes in the casing that frustratingly leak gearbox oil - can’t they Matt?

Sent from my iPhone using Tapatalk