After the last top end rebuild of my engine a couple of years ago, this spring, I decided it was time for a little work on the engine and I decided to add a pair of EMPI HPMX 40s to my build. I thought to myself, 'this should only take me a weekend or so, drop the engine, whip the heads off and have a look around, give the valves a lapping and re-fit, back together with the new carbs, hey presto'
Then, I thought, while i'm doing the carbs, i'm going to fit proper braided fuel hoses, so £250 or so later.... this arrives
So, then, I thought, 'while i've got the heads off, why not go for 1641 barrels and pistons?' So, with the parts ordered and arrived, the rebuild began....
And all was going great, 1 & 2 back together, valves lapped, head back on and torqued down, 3 & 4 became another story in itself, cos after lapping the valves, I went to put the head back on, and 2 of the head studs pulled straight out of the case. I couldn't even get 7 ft/lb on the torque wrench on them, just kept pulling and pulling, eventually pulling both of the case savers out with a nice little thread of ali embedded in the case saver.
After a quick call to Cool Air, it turns out that I have the largest case savers already installed (14mm) so, i'd resigned myself to it being a new case job. This is the part where it gets interesting.....
I've never split a case before, so after removing lots of nuts, my old case was split...
To find this:
With the corresponding groove worn into the crank main bearing journal.
I will add to this story as it progresses...
Then, I thought, while i'm doing the carbs, i'm going to fit proper braided fuel hoses, so £250 or so later.... this arrives
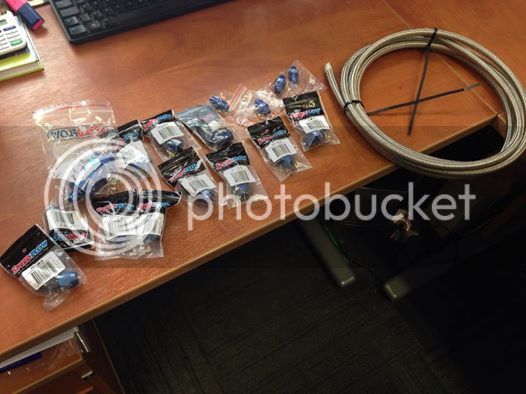
So, then, I thought, 'while i've got the heads off, why not go for 1641 barrels and pistons?' So, with the parts ordered and arrived, the rebuild began....

And all was going great, 1 & 2 back together, valves lapped, head back on and torqued down, 3 & 4 became another story in itself, cos after lapping the valves, I went to put the head back on, and 2 of the head studs pulled straight out of the case. I couldn't even get 7 ft/lb on the torque wrench on them, just kept pulling and pulling, eventually pulling both of the case savers out with a nice little thread of ali embedded in the case saver.
After a quick call to Cool Air, it turns out that I have the largest case savers already installed (14mm) so, i'd resigned myself to it being a new case job. This is the part where it gets interesting.....
I've never split a case before, so after removing lots of nuts, my old case was split...

To find this:
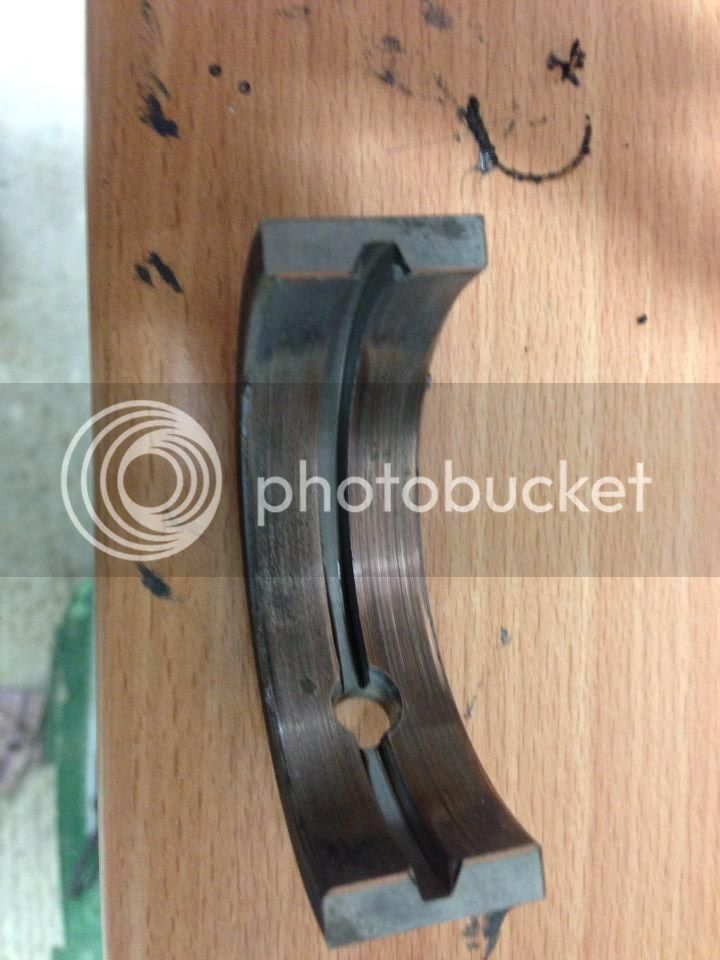
With the corresponding groove worn into the crank main bearing journal.
I will add to this story as it progresses...